Plastic pollution is a global issue with major environmental consequences. According to the UN Environment, researchers estimate that more than 8.3 billion tonnes of plastic have been produced since the early 1950s. About 60% of that plastic has ended up in either a landfill or the natural environment, and if that trend continues, by 2050 our oceans could contain more plastic than fish. The good news is that people, governments, and some companies have been taking some actions, that’s why we are dedicating our Eco Maven section of February to a company that is creating positive change on that front.
MacRebur, a British-based company that manufactures waste plastic road solutions will be launching in the U.S. market soon and gave Eco18 some insights into the work they do and how they came about the idea of creating roads made of plastic. Here are Toby McCartney, co-founder, and CEO of MacRebur responses to our questions on the subject.
1) What’s your name and your role at MacRebur?
My name is Toby McCartney, and I am the co-founder and CEO at MacRebur.
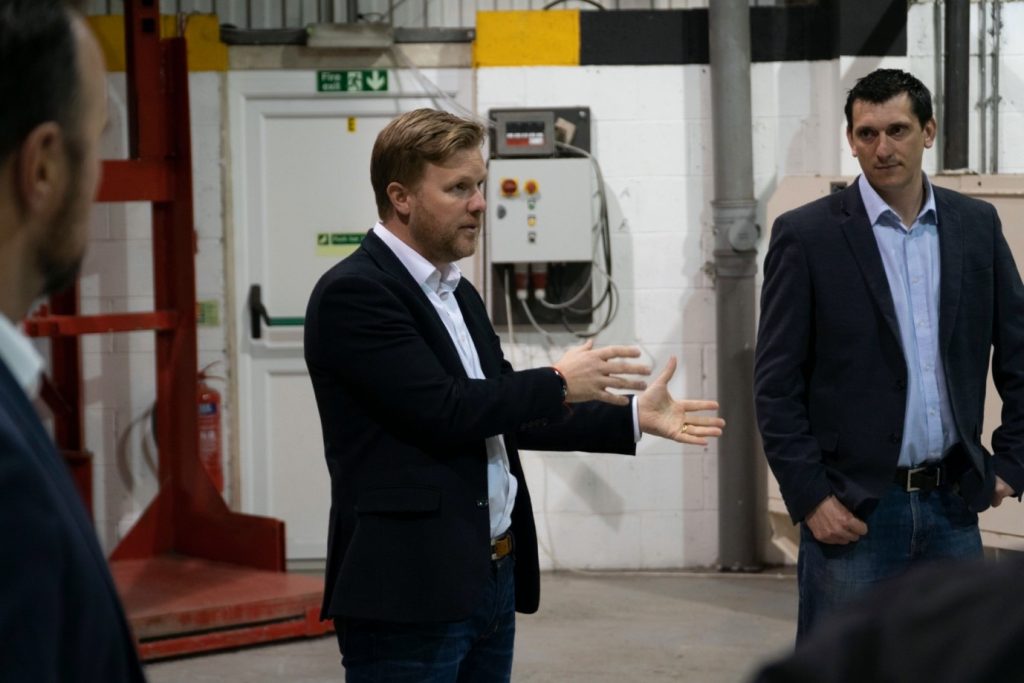
2) Tell us more about the non-recyclable waste plastic roads that your company manufactures?
We process waste plastics otherwise destined for landfill or incineration and add them into asphalt for road construction. Enhancing and extending the bitumen (fossil fuel) binder, this improves the quality of the road whilst helping resolve the waste plastic epidemic.
For each mile of road laid using our product, it uses up the equivalent of 1,194,421 one-time use plastic bags, with one ton of MacRebur mix containing the equivalent of 80,000 plastic bottles.
3) How did the idea of creating roads made of plastic come about?
I came up with the idea whilst working in Southern India with a charity that helps people who work on landfill sites as “pickers”. The job of a picker is to gather potentially reusable items and sell them on to be turned from rubbish into something useful again.
Some of the waste plastics retrieved by the pickers were put into potholes, diesel poured all over them, and the rubbish set alight until the plastics melted into the craters to form a makeshift plastic pothole filler.
I thought this was a brilliant idea, though would likely be ‘frowned upon’ back in the UK! So, I got together with two friends, Nick and Gordon – the co-founders of MacRebur – and we spent 18-months testing and trialling to find a way to safely use waste plastics in our roads.
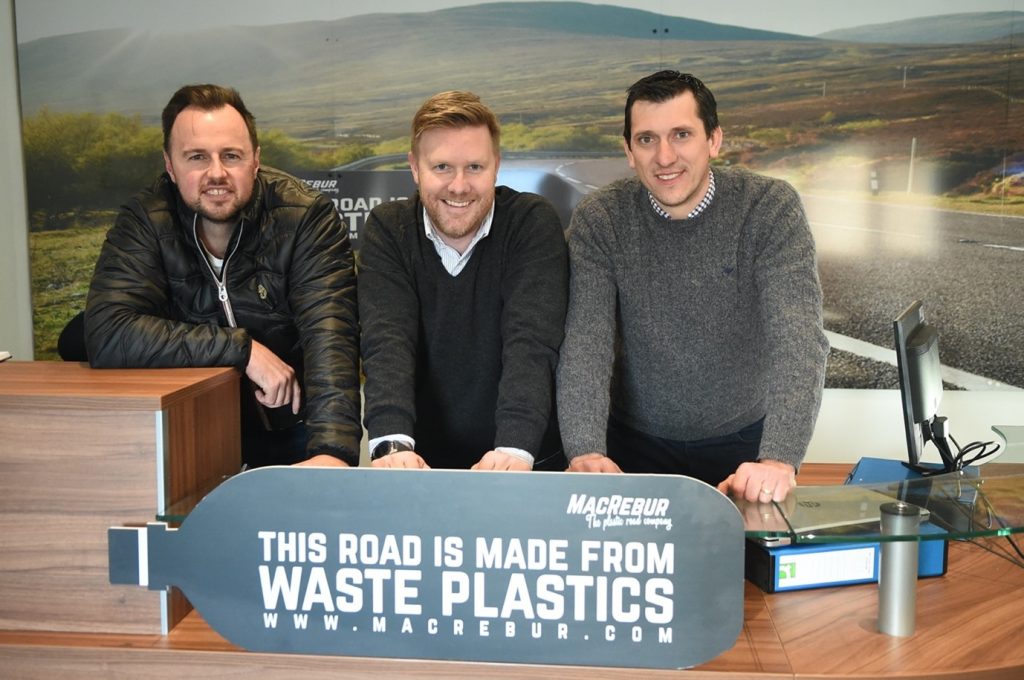
4) What other components are used in these plastic roads?
We carefully select the waste plastics that we use and have a strict quality control procedure before they are used to make up part of our mix. The waste plastic is blended in with our specially designed activator – it’s this that makes the plastic bind properly into our roads, but what is in it is a company secret!
5) Are there other benefits from the plastic roads, aside from the use of non-recyclable waste plastics?
We enhance the quality of the bitumen binder and the end product of the asphalt. By using the brilliantly engineered quality of a polymer we can enhance the road in many ways – making it more flexible and less susceptible to rutting for example. That means they can cope better with contraction and expansion caused by changes in the weather, reducing cracks and resulting in less potholes and road repairs.
MacRebur roads can also be cheaper to manufacture because we are extending the bitumen, or oil, with waste that has little or no value.
6) How does it look like? Any particular color or texture?
Our roads look exactly the same as regular asphalt!
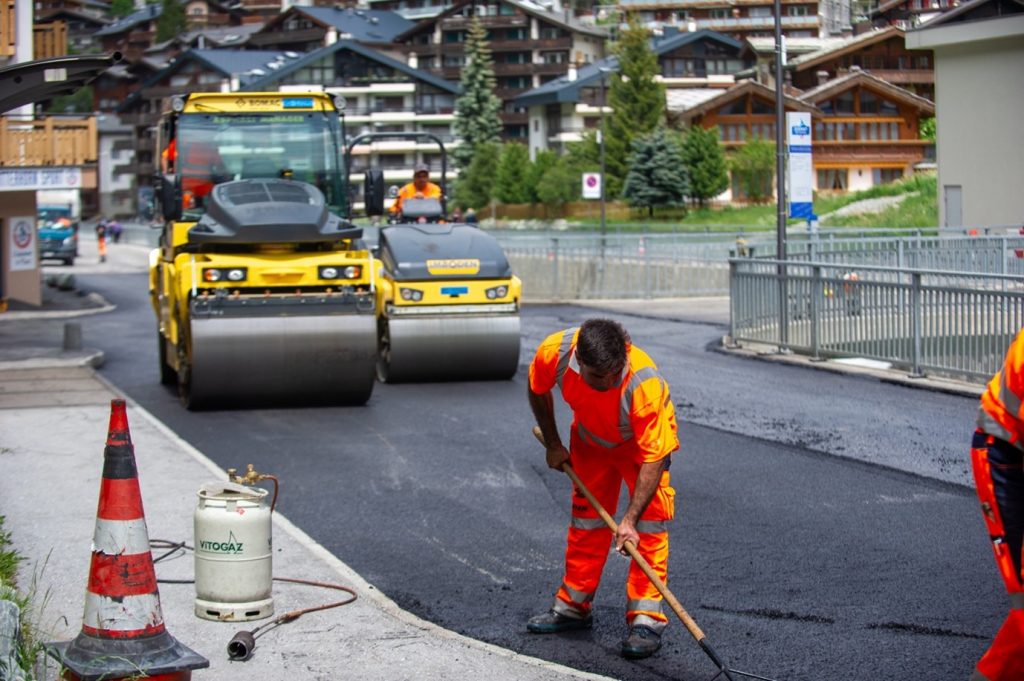
7) What are the costs associated with the plastic roads vs. the traditional ones? Is it cost effective?
As mentioned above, our roads can be cheaper to make because we’re using waste that has no value and use.
We use local waste for local roads in many countries. We use waste that would otherwise be going to landfill or for incineration – where there is often a cost for it to be disposed of – so it’s a win-win for everyone involved in MacRebur’s plastic roads.
8) What is the durability of the plastic roads?
It has been demonstrated by various laboratories across the world that our roads significantly improve the stiffness and deformation resistance of asphalt, whilst avoiding the embrittlement of oxidisation, evidenced by increased fracture toughness and fatigue life.
9) Does it require a special maintenance process?
There is no maintenance process for our roads. In fact, because our products improve the quality of the road, you could argue it needs less maintenance compared to traditional roads!
10) Where do you get the plastic?
We take plastic waste which is generated from typical industrial, commercial and household use. These are a carefully selected range of polymers normally deemed for landfill or incineration.
11) What are some of the clients that MacRebur has worldwide?
From the world-renowned Gleneagles Hotel in Scotland, to the Olympic Park in London, you can find our roads everywhere from the UK, to Australia, South Africa and Dubai.
You can find also MacRebur roads in Zermatt, one of the world’s most iconic destinations, UC San Diego, New York with Itinera Infrastructure and Concessions, Saudi Aramco in Saudi Arabia and in most countries around the world.
12) How do you think this solution can help the U.S. market?
With 38 million tons of plastic finding its way to landfill each year in the US, building MacRebur roads across the country could help reduce this number; utilizing the waste plastic while helping to foster a circular economy.
Plastic packaging is a huge problem in the U.S. and a large contributor to the 80 million tons of waste being produced every year. This troubling statistic presents us with an opportunity to offer a green alternative to a growing problem.
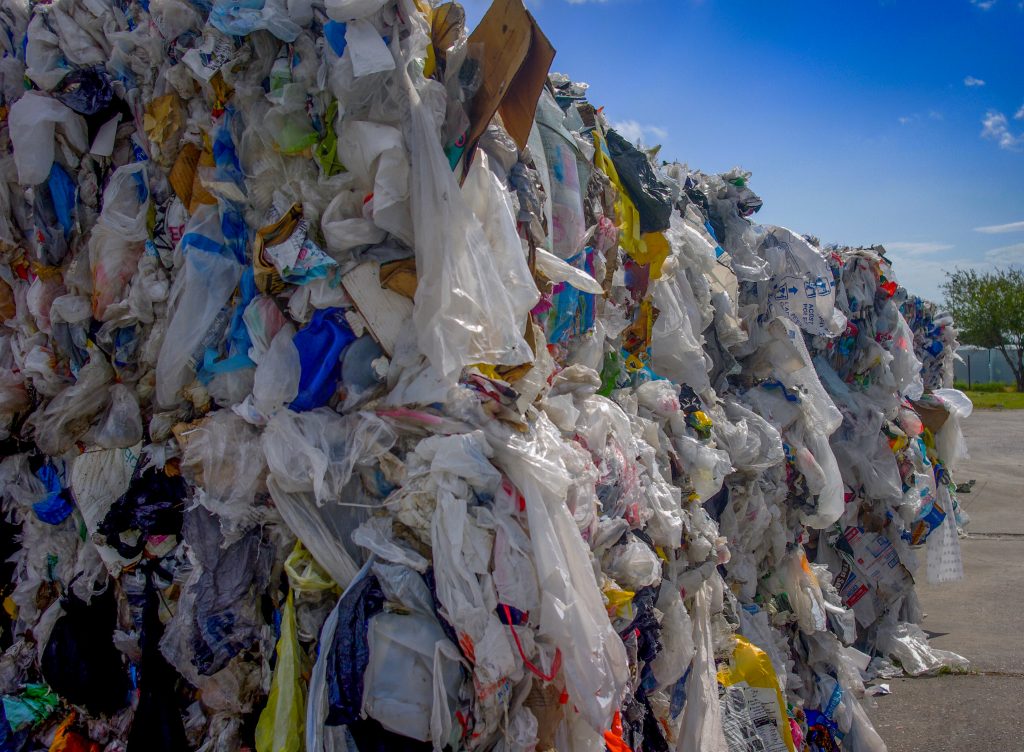
13) When are you planning to launch in the United States?
We have a site already located with partners in San Diego, California, and have plans for our own MacRebur owned site in Florida towards the end of this year. It’s exciting times for MacRebur USA.
14) We understand that you will be opening your offices in FL, how many people would you be employing?
Our first factory in FL will take on up to 15 members of staff once up and running, with potential to expand in the near future.
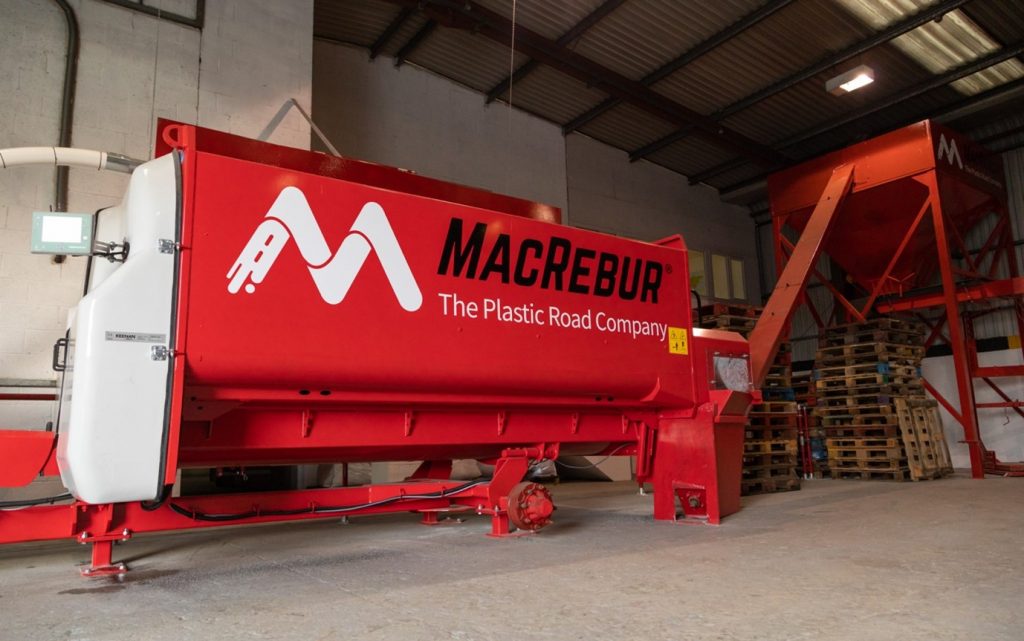
15) Are you planning on expanding your presence in the U.S. after the launch in FL?
We are also currently looking at areas in Texas and Maryland to further expand in the U.S. once up and running in FL.
16) Is it possible to solve the waste plastic epidemic in the U.S. with this solution?
Not completely to be perfectly honest – the waste plastic epidemic is so huge – but we are certainly a step towards the solution.
17) This is an exciting time to initiate operations in the U.S. Do you have any projections of the success of the business in America?
Exciting indeed. We believe 2021 will be a great year for MacRebur USA and have high hopes for our business and partner’s businesses over the next three-year roll out.
18) How do you see the future of sustainability in the world?
We have a long way to go in convincing some of our government officials to not simply talk about the problems but take action with the innovative solutions available to them.
We are able to offer some of our services for free to them because of the importance of our innovation, but even when it comes free, there’s still a huge amount of resistance for change from some.
I hope that every business and government authority will implement some environmental and social change innovations into their business. Creating win-win solutions is the only way forward!